LOTO: виграють всі
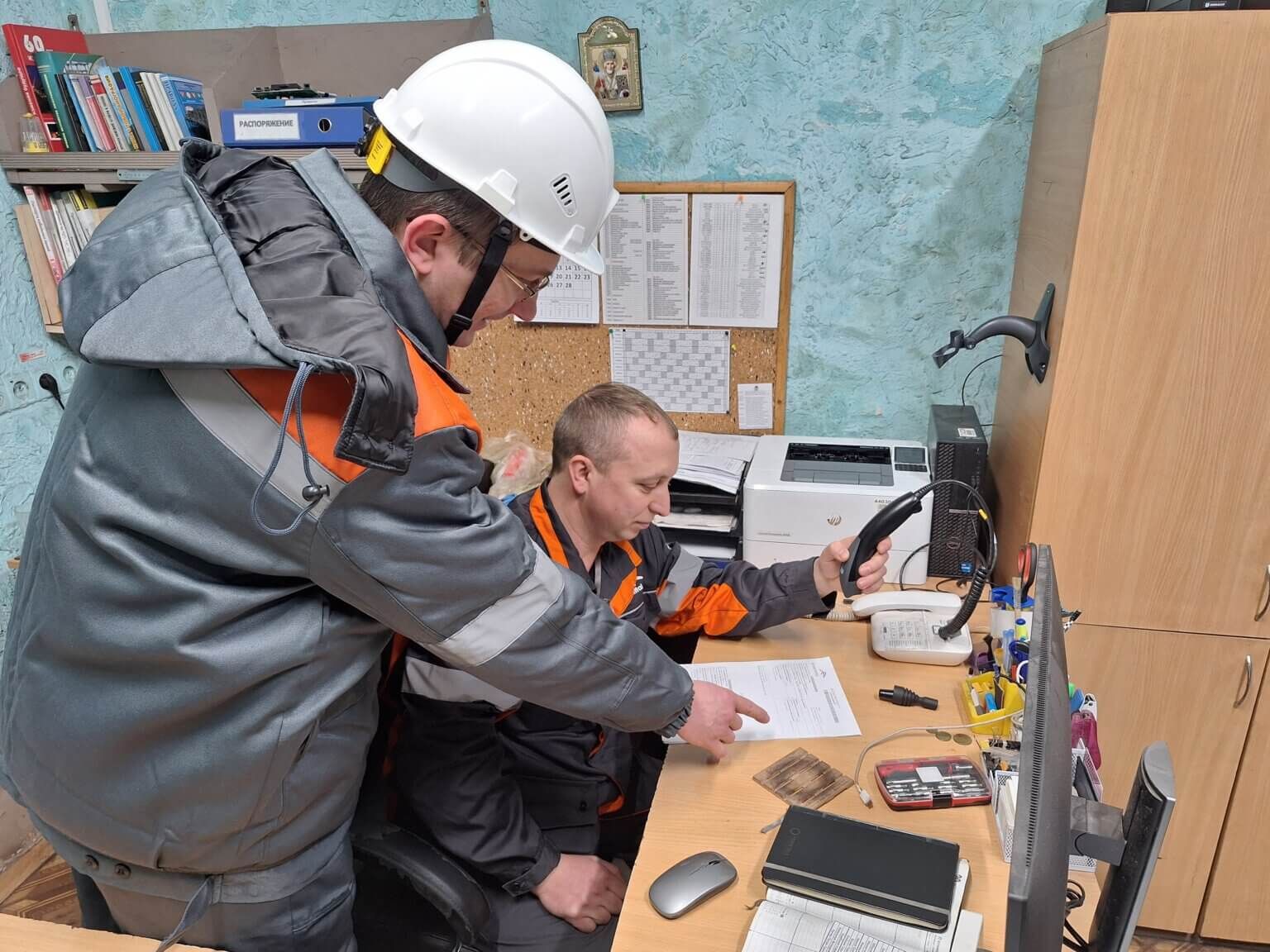
Сортопрокатний цех № 2 має успіхи у вдосконаленні застосування системи блокування небезпечних енергій LOTO, що робить ремонти безпечнішими та скорочує підготовку до них.
Прокатний цех – це комплекс складного й потужного устаткування (електричного, механічного, енергетичного) для виробництва металопрокату. Його елементи рухаються, обертаються за рахунок електроенергії. Трубопроводами до вузлів подаються енергоресурси. Для попередження запобігання аварійним зупинкам на прокатних станах регулярно проводяться планово-попереджувальні ремонти (ППР). Щоб заблокувати небезпечні енергії під час ремонтів, використовується система LOTO. Для більшої ефективності та спрощення її використання вирішили використати можливості системи SAP.
«Перед кожним ремонтом необхідно застосувати комплекс заходів з блокування/ізоляції небезпечних енергій для того, щоб випадкове вмикання струму, механічного устаткування чи подачі пару або іншого енергоресурсу під час виконання ремонтних робіт не призвело до трагедії, – розповідає менеджер ARMP Валентин Машошин. – Тож перед кожним ППР або іншим ремонтом визначалися ризики, точки їх блокування, ретельно планувалася взаємодія між ремонтниками електро-, енерго-, механослужб та підрядних організацій, які виконують роботи, довго оформлялися та складали наряд-допуски і дозвільні документи на паперовому бланку. Це займало багато часу, а так званий людський фактор безпеки не додавав, бо від помилки ніхто не застрахований. Тож було вирішено зібрати всю інформацію про ризики та способи їх блокування на всіх ділянках, створити бібліотеки (масиви електронної інформації) та помістити їх у систему SAP, де зберігається і трансформується інформація про роботу підприємства та його підрозділів».
Збір інформації стартував на початку минулого року. Працівники СПЦ-2 дослідили місця проведення планово-попереджувальних ремонтів від нагрівальних печей до ліній пакування, виявили і описали ризики, визначили точки та способи блокування небезпечних енергій. А їх колеги зі служби ARMP створили покрокові інструкції блокування небезпечних енергій для основних видів ППР і помістили потрібну інформацію до системи SAP.
«Зараз нам не треба перед кожним ремонтом наново вивчати ризики, визначати точки, способи і порядок блокування, – розповідає старший майстер з ремонту електроустаткування СПЦ-2 Олексій Тихомиров. – Дякуючи електронним бібліотекам в SAP ми, представники всіх ремонтних служб та підрядників, отримуємо чітко прописаний порядок дій – що, де і коли блокувати. Користуючись цією інформацією, представники різних служб встановлюють на відповідних місцях свої блокувальні пристрої і замки, і поки триватиме ремонт, вже ніхто не зможе відновити подачу електроенергії, газу, пару чи будь-якого іншого енергоресурсу, або увімкнути, наприклад, гідравлічне устаткування. Поки всі бригади не покинуть місце ремонту, а кожен з керівників ремонтних підрозділів (а якщо бригад небагато і вони невеличкі за чисельністю, то й кожен учасник ремонту) не зніме свій замок, електрик не зможе відновити подачу струму. Принцип «одна людина, один замок, один ключ» діє безвідмовно. Надійно на сто відсотків!»
Як розповів начальник СПЦ-2 Олександр Макаренко, застосування автоматизованої системи підготовки до ремонтів за допомогою інструментів SAP SAFETY дозволяє скоротити час підготовки до ремонтів від кількох годин до години у середньому, що підвищує продуктивність роботи цеху за рахунок скорочення часу на ремонти.
«Але головне – це підвищення рівня безпеки для людей, – говорить Олександр Макаренко. – Ми починали з 80-ти одиниць устаткування. А зараз працюємо вже з понад 220 одиницями. Роботи зі створення бібліотек інформації в SAP вже завершені на 80 відсотків. Процес триває. Закуповуються додатково нові моделі блокувальних пристроїв для застосування LOTO в повному обсязі. Закуповуються принтери, за допомогою яких можна швидко роздрукувати дозвільні документи, які вже сформовані у SAP SAFETY. Не дивлячись на складні умови в наш час, пріоритетом номер один на нашому підприємстві залишаються безпека праці і життя працівників»