Козлів в ковшах не має бути
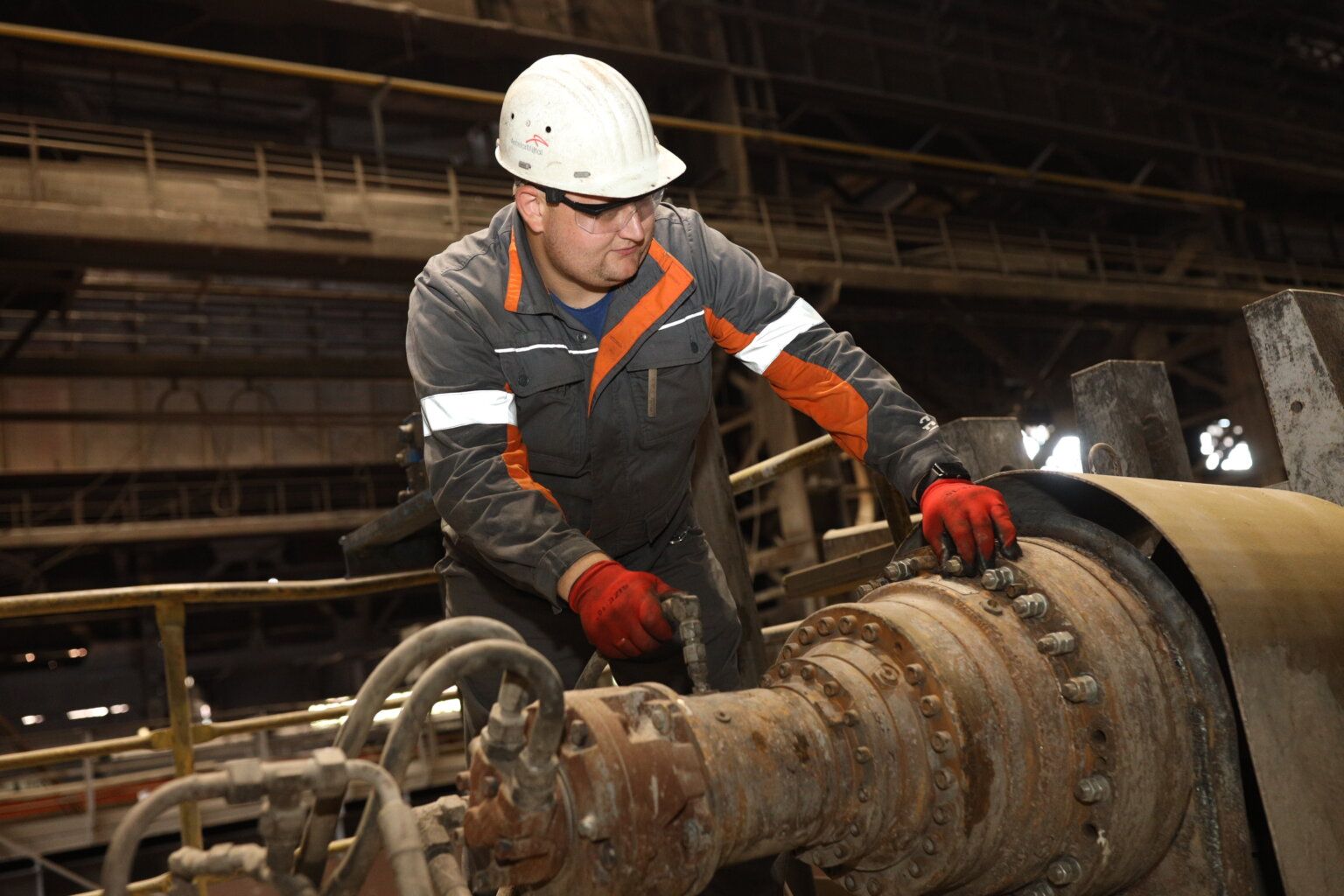
У відділенні проміжних ковшів конвертерного цеху відновили до базового стану унікальну машину, без якої неможливе безперервне розливання сталі.
Проміжні ковші (промковші) – важливе устаткування для безперервного розливання сталі. Кожен промковш може вмістити 30 тонн сталі. Промковш ламає стереотипи про форму металургійного ковша. Він зовсім не схожий на циліндричний кухоль, і якщо дивитися згори, то має форму неправильного витягнутого чотирикутника з носиком. Це зумовлено його функцією. У нього заливають сталь із сталерозливального ковша одним струменем, а з промковша сталь ллється вже шістьма окремими струменями для формування шести сталевих заготовок. Після розливання у ковші залишаються залишки сталі, вони вичахають, стають твердими (їх ще називають козлами), і для видалення цих козлів застосовується машина витискання промковшів.
За словами інженера WCM Олександра Шніткова, на роботу машини витискання останнім часом було чимало нарікань.
«Сама машина складається з рами, на яку встановлюється та кріпиться промківш; шести гідравлічних циліндрів, які через отвори ковша витискають залишки сталі; гідравлічної станції, що приводить в рух гідравлічне устаткування, яке обертає раму на 360 градусів та приводить в дію гідравлічні циліндри. – розповідає Олександр. – Навантаження на машину надзвичайно велике, а ще корозія, тож вона була добряче «приморилася», часто виходила з ладу. А це неприйнятно, адже розливання сталі безперервне, тож промковші треба постійно чистити від залишків сталі, готувати до розливання наступних серій плавок та своєчасно подавати на МБЛЗ. Для відновлення стабільної роботи машини ми вирішили застосувати автономне обслуговування Виробництва світового класу WCM».

Роботами з автономного обслуговування машини керував майстер з ремонту устаткування конвертерного цеху Михайло Кириченко.
«Слюсарі-ремонтники Вадим Яковенко та Дмитро Верес, зварник Юрій Шаєнко, технік Дмитро Кушим, в.о. майстра Юрій Бакаліна за відносно невеличкий проміжок часу виконали значний обсяг робіт, і позитивні результати вже є, – говорить Михайло Кириченко. – Здавалося б просте рішення – встановити кнопку пуску машини на пульті керування. Раніше її не було. Працівникові, який керує витисканням промковша, доводилося спускатися сходами, потім проходити певну відстань, щоб увімкнути машину, ну а потім таким же чином вертатися на пульт. А якщо треба оглянути ківш зсередини, то треба йти вимикати машину і знов вмикати. Люди втрачали час та енергію. Ми встановили кнопку, якою машина вмикається з пульта».
Також Михайло розповів про проблеми з редуктором, який обертає раму. Раніше він був закріплений не надто надійно, що створювало проблеми, призводило до вимушених зупинок машини. Металоконструкції, на яких кріпиться редуктор, підсилили, наваривши додаткові елементи, а також підсилили шпилькові з’єднання, що утримують редуктор на металоконструкціях. Наразі аварійних зупинок, пов’язаних зі зміщенням редуктора, немає. Гідравлічну станцію, яка розташовувалася так близько до робочої зони, що в неї потрапляли козли, витиснуті з промковшів, перенесли на кілька метрів з врізанням додаткових трубопроводів. А для захисту ще й встановили захисну огорожу. Тепер захищені як сама станція так, і люди, які її обслуговують. Також замінили шафу керування станцією, а з’єднання кабелів сховали у захисні коробки.

Старший майстер вогнетривного відділення конвертерного цеху Дмитро Левицький відповідає за своєчасну підготовку промковшів для відділення безперервного розливання сталі. «Очищення ковшів від козлів – важливий етап їх підготовки. В результаті впровадження автономного обслуговування працювати з машиною нам стало набагато зручніше та безпечніше. А суттєве зменшення аварійних простоїв дозволяє швидше і якісніше виконувати свою роботу».
Але автономне обслуговування не усунуло всіх проблем. Як пояснив технік Дмитро Кушим, проблемною залишається ситуація з гідравлічними циліндрами. «На жаль, у нас немає резерву циліндрів, а дуже хотілося б, – каже Дмитро. – Тоді б ми змогли провести ревізію тих циліндрів, які у нас є. Ми розуміємо, що зараз складне фінансове становище, а нове устаткування потребує коштів. Але логіка вказує на те, що на простоях, вимушених ремонтах та витоках гідравлічної рідини ми з часом втратимо більше, ніж коштують циліндри».

Олександр Шнітков зазначив, що команда WCM вже взялася за вирішення цієї проблеми. «Ми виявили основні причини виходу гідроциліндрів з ладу і пропонуємо модифікувати їх. Департамент з виробництва чавуну і сталі підтримав нас. Доцільно було б закупити саме модернізовані циліндри. Передбачається, що їх використання допоможе значно скоротити витрати на ремонти, розхідники та зменшити простої. Розрахований економефект – 540 000 грн».
Відновити устаткування – це пів діла. Необхідно ще й утримувати його у базовому стані. А для цього у WCM передбачені стандартні операційні процедури (СОП). Саме зараз розробляються СОПи. Фактично це інструкції, як обладнання своєчасно та якісно інспектувати, чистити, змащувати та обтягувати кріплення. Адже тоді воно працюватиме значно довше.
