WCM: на межі десятиліть
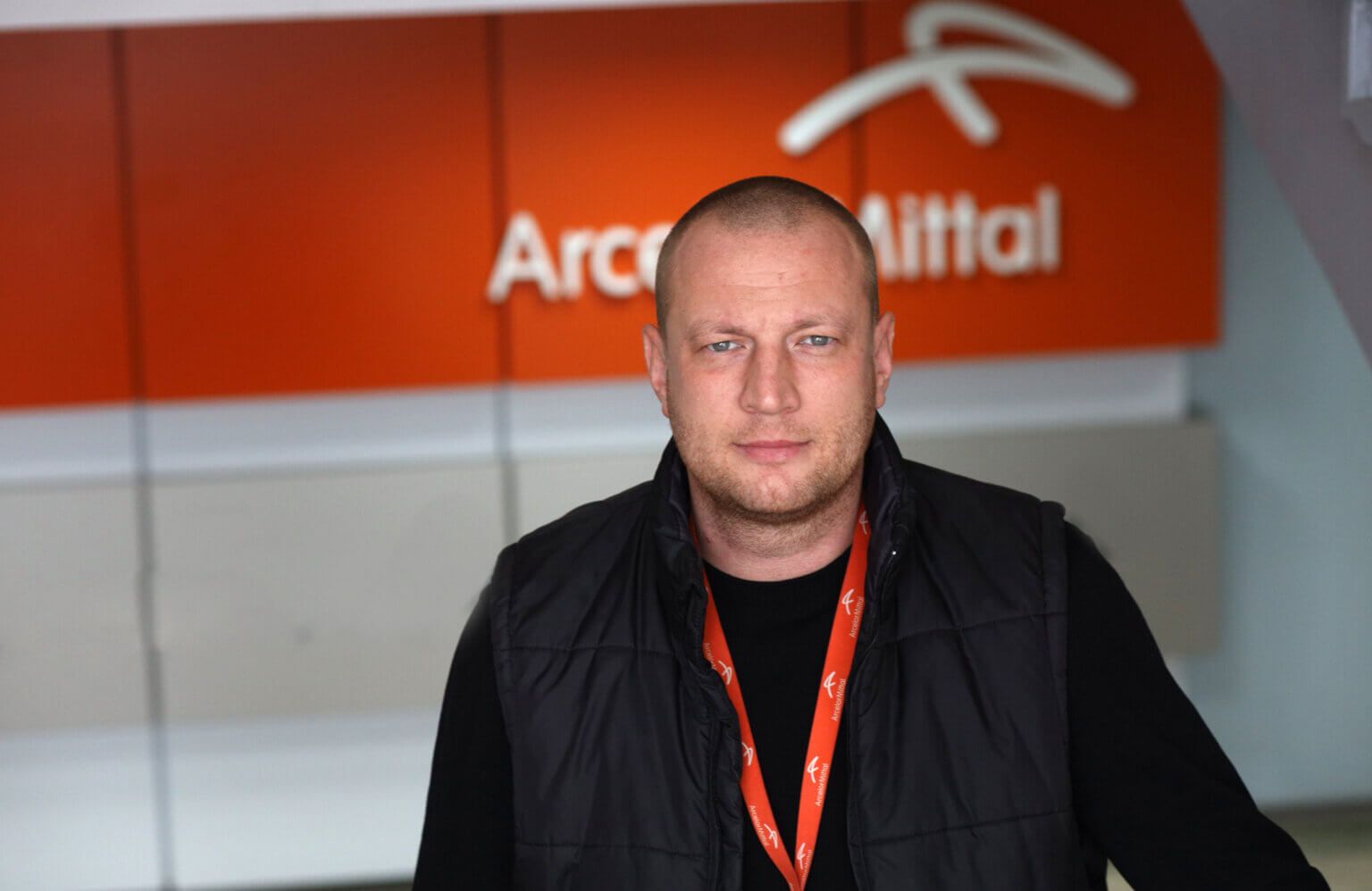
Виробництво Світового класу (WCM) впроваджується в «АрселорМіттал Кривий Ріг» вже понад десять років. Економічний зиск від його впровадження з 2013 по 2024 рік склав близько 275 млн доларів США (на підставі погодженої службою промислового контролінгу вартості втрат), а скільки було усунуто ризиків важко й підрахувати. Попри повномасштабне вторгнення й пов’язані з ним негаразди, команда продовжує роботу над покращеннями. Про це й не тільки – у інтерв’ю з в.о. керівника з впровадження WCM Олексієм Можако.
– Олексію, на що зараз спрямована робота команди WCM?
– Як завжди, ми націлені на скорочення витрат на виробництво продукції, зростання її якості та створення безпечніших умов для працівників. Для цього працюємо за кількома напрямками, які, нагадаю, називаються колонами: професійне та автономне обслуговування обладнання, спрямовані покращення, розвиток персоналу, охорона праці та інші. Підвищення надійності роботи устаткування – один з основних моментів, бо коли воно ламається, знижується продуктивність, і зростають витрати на ремонти. Усунення ризиків для життя й здоров’я людей – серед найважливіших напрямків. Розвиток персоналу, набуття нових вмінь, навичок та знань сприяють продуктивнішій та безпечнішій роботі. І все це ми втілюємо разом із працівниками структурних підрозділів.
– Які здобутки команди у 2024 році?
– Впроваджено багато покращень. З тих, які зразу спадають на думку – проєкт «0 поломок» у доменному цеху № 1. Там були проблеми з роботою шибера. Якщо по простому, то це велика заслінка, яка випускає гаряче дуття та гази під час планово-попереджувальних ремонтів доменної печі. Вона не завжди щільно прилягала при закритті. З-за цього доменники мали значні додаткові витрати часу на поновлення виробництва чавуну, так звану задувку. Була розроблена конструкція додаткового змійовика, який охолоджує шибер та кладку. Як результат – шибер вже майже шість тисяч годин працює без збоїв, що на цей момент зекономило підприємству понад 20 тисяч доларів.
А у кисневому виробництві, яке поки що на простої, скористалися моментом і впровадили зміни, які зможуть захистити устаткування під час можливих блекаутів. Там для роботи важливих вузлів компресорних установок постійно потрібно змащувати підшипники. Якщо ж миттєво вимкнути подачу електроенергії, то насоси не зможуть подавати мастило, і поки елементи, які набрали шалених обертів, зупиняться, то внаслідок тертя без мастила коштовне устаткування вийде з ладу. Підраховано, що для його відновлення у такому випадку знадобиться близько 170 тис. доларів. Не зважаючи на зупинку виробництва, керівник цеху Володимир Черногоров ухвалив рішення про подальше впровадження усіх напрямків WCM. Одним з найважливіших для підрозділу став 10-кроковий проєкт WCM, в ході впровадження якого розробили й змонтували систему, що дозволить самопливом подавати мастило на підшипники у разі зупинки насосів.
Або, наприклад, проєкт з охорони праці в управлінні залізничного транспорту гірничого департаменту. Виготовлення та використання спеціальних упорів-стопів під час ремонтів і обслуговування напіввагонів з піднятим кузовом дозволило повністю усунути ризик травмування, якщо кузов самовільно опуститься. Якщо підсумувати, то при плані скорочення витрат на 12,2 млн доларів у нас вийшло скоротити їх на 10,5 млн.
– Що ж завадило виконати план з скорочення витрат на сто відсотків?
– Дійсно, є перелік об’єктивних причин. Найперше – ми впроваджуємо проєкти як на працюючому устаткуванні, так і на тому, яке зараз тимчасово у простої з-за обмеженого попиту на продукцію та обмеженої здатності її виробництва з причин, викликаних великою війною, . У таких випадках ми просто не можемо відслідкувати економічний ефект на непрацюючому устаткуванні, і він не йде до загальної скарбнички. А ще в умовах обмеженого фінансування, викликаного важким становищем підприємства, ми впроваджуємо, перш за все, найважливіші, найнагальніші заходи.
Ще одна причина: нам доводиться не лише втілювати зміни, а ще й у процесі формувати нову команду. Зараз близько половини фахівців із впровадження WCM захищає нас зі зброєю в руках. Наш керівник Святослав Кузьменко пішов добровольцем у перший же день вторгнення, як і Олександр Пшеничний, який, на жаль, загинув. Він був не лише нашим колегою, а й другом. Завжди його пам’ятатимемо. У лавах ЗСУ і наступник Святослава Олег Шорохов. Ми підмічаємо у цехах вмотивованих працівників, підтягуємо у свою команду, одразу ж і навчаємо, бо Виробництво світового класу – це складна наука з безліччю засобів, методів та інструментів покращення.
– І нарешті, традиційне питання: які плани на цей рік?
– Плани – вдосконалювати надалі і самим вдосконалюватися, попри всі негаразди. Зараз команда працює над «Розкладанням витрат», як воно зветься у нашій методології. Тобто, ми аналізуємо виробничі втрати минулого року, визначаємося з найпроблемнішим устаткуванням, надійність, стабільність роботи якого необхідно терміново підвищувати. Працюємо над тим, щоб довести доцільність капіталовкладень у той чи інший проєкт, і зараз це непросто.
Традиційно завершили рік серією тренінгів з Виробництва світового класу. Його пройшли близько 120 працівників цехів – керівників цехових команд та голів колон, та й будь-хто з охочих міг взяти участь. Метою було ознайомити наших партнерів-цеховиків з можливостями системи та з основними інструментами, які допоможуть реалізувати ці можливості. Працюємо далі. У скрутні часи скорочення витрат, економне виробництво стають ще актуальнішими. А безпека людей – завжди у пріоритеті».