«Зелене світло» для азоту
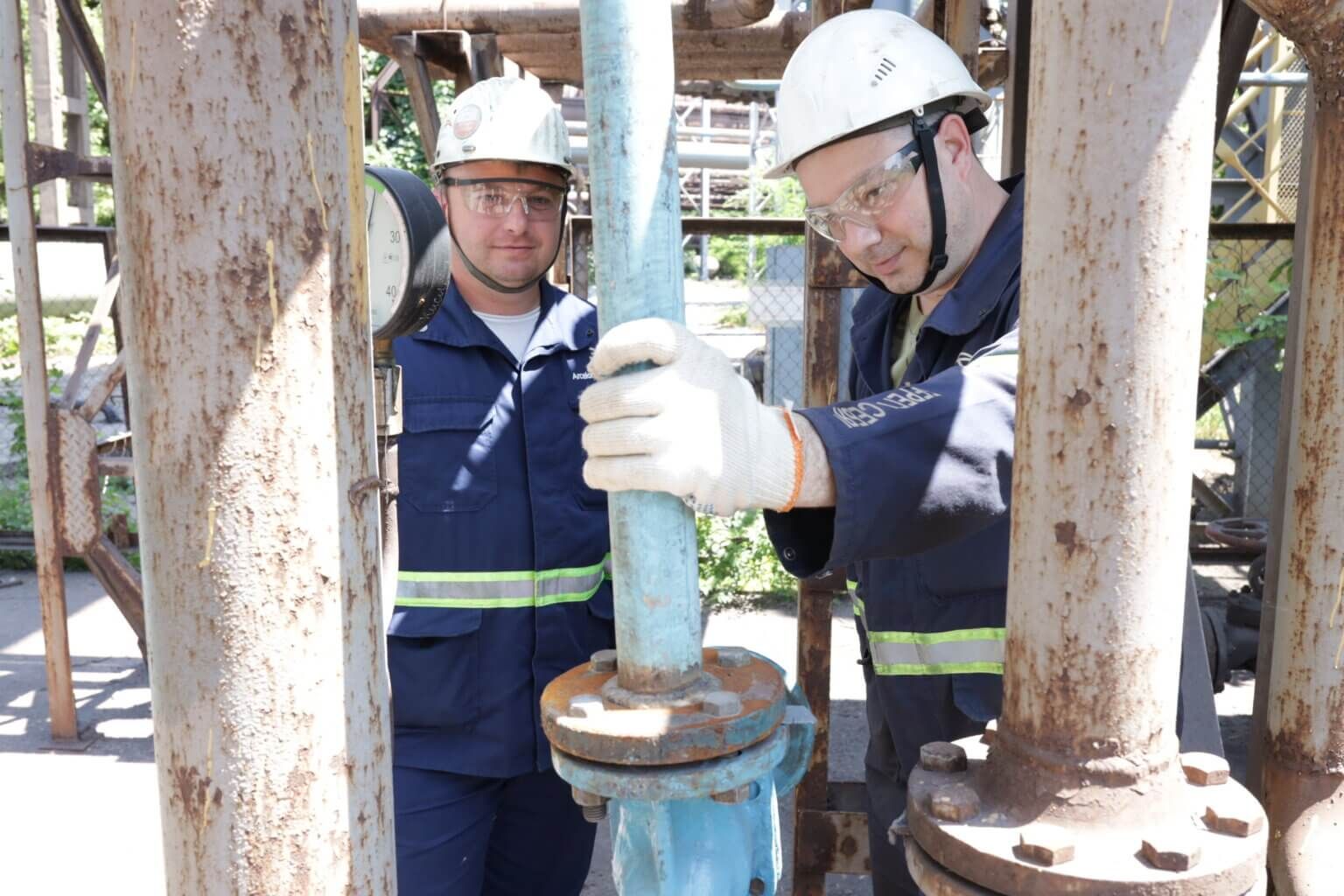
Працівники цеху з ремонту енергетичного устаткування виконали ремонт та перепідключення 3,5 км азотопроводу.
Робота нагрівальної печі дрібносортного стану неможлива без такого компоненту, як азот. Зазвичай його постачає наше кисневе виробництво. Але під час блекаутів з цим виникали проблеми. Виробничники почали шукати вихід. «Батьками» рятівної ідеї стали фахівці з енергодепартаменту та кисневого виробництва «АрселорМіттал Кривий Ріг», а от втілили ідею в життя ремонтникицеху з ремонту енергетичного обладнання центрального департаменту з утримання та ремонтів .
«Ми розуміли, що від роботи азотопроводу залежить безпека персоналу, який працює на печі на ДС 250-4, – говорить начальник кисневого виробництва Володимир Черногоров. – Нам потрібен був діючий азотопровід, яким би азот надходив до дрібносортного стану безперебійно, незважаючи на блекаутні сюрпризи. Для цього потрібно було виконати ремонт та підготувати азотопровід. Завдання не з легких, і довірити його можна було лише справжнім професіоналам. Щоб втілити ідею в життя, ми допомогли ремонтникам з організацією транспорту для виконання робіт (використовувалися автовишка, автокран), знайшли необхідні матеріали для ремонту. Ми як замовники виконаною роботою задоволені на всі сто. Азотопровід вже у роботі».
Роботи проводилися на ділянці довжиною 3,5 км. Азотопровід місцями проходить на висоті, є багато ділянок, до яких складно дістатися. Щоб надати «зелене світло» для руху азоту цим азотпроводом, довелося чимало попрацювати.
«Наш цех завжди готовий виконати завдання, які за великим рахунком нам «не притаманні», які ми раніше не виконували. Ми – цех-експериментатор, – говорить заступник начальника ЦРЕУ Олександр Шаховий. –У цієї конкретної задачі були кілька ускладнюючих факторів, але найголовніше, що вимагав цех-замовник – швидкого та якісного виконання робіт. Азотопровід вироблений з неіржавіючого металу, раніше використовувався за іншим цільовим призначенням. Довелося буквально «пазли» збирати. Ми певні ділянки газопроводу вирізали, перезварювали, встановлювали на інші місця, фактично перепідключали азотопровід. Усі роботи виконували досвідчені газозварники. У деяких місцях варити доводилося на висоті до 10 метрів, тож задіяли і автокран, і автовишку. Але траплялися такі хитромудрі місця, куди автовишкою не під’їхати. Але ми з усіма викликами впоралися. Перевіркою нашою роботи стало опресування – це коли повітря подається азотопроводом завищеним (у порівняні з робочим) тиском. Це перша перевірка надійності та якості виконаних робіт. Натиск азотопровід витримав, і це підтвердило, що якість стиків та зварних швів була на найвищому рівні. За це дякую всьому персоналу нашого цеху, особливо майстру з ремонту обладнання Олександру Шаповалу та електрозварнику Олександру Гриньову».
