Коксові батареї: історія, збудована з нуля
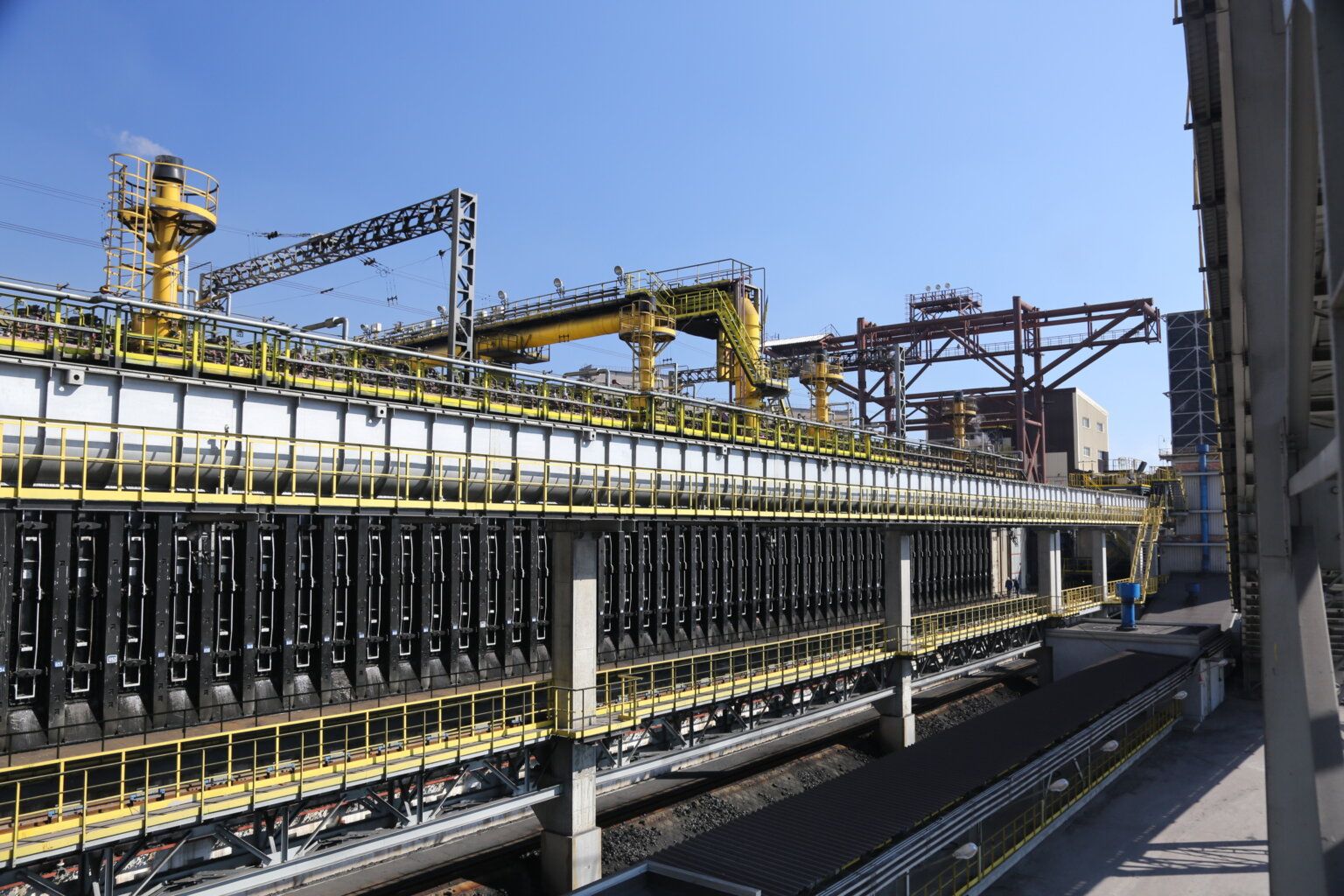
«АрселорМіттал Кривий Ріг» – єдине металургійне підприємство в Україні, яке за роки незалежності збудувало нові коксові батареї збільшеної потужності з сучасними технічними рішеннями та з мінімальним впливом на екологію. У рубриці «20 років разом» ми згадаємо, як відбувався цей процес, на що робився акцент, як працівники вчилися керувати обладнанням, а згодом рятували КБ від несподіванок та випробувань війни.
Цього року ми відзначаємо 20-річчя з моменту приходу компанії «АрселорМіттал» в Україну. Корпорацією одразу було розпочато процес модернізації виробничих потужностей нашого підприємства. Інвестиції компанії були спрямовані на покращення екології, умов охорони праці, оновлення виробництва.
Одним із наймасштабніших інвестиційних проєктів стала реконструкція коксових батарей №№ 5 та 6, на яку компанія «АрселорМіттал» спрямувала більш ніж 160 млн доларів. Фактично відбулось будування коксових батарей «з нуля». У цього проєкту було декілька цілей – здійснення екологічних заходів, які дозволять в рази знизити викиди забруднюючих речовин в атмосферу, а також забезпечення додаткового виробництва власного коксу та коксового газу, для зниження обсягу покупного коксу та природного газу.

Як все починалось
25 травня 2018 року. Це особлива дата в історії компанії «АрселорМіттал», нашого підприємства, міста, а також усієї країни. ПАТ «АрселорМіттал Кривий Ріг» урочисто відкрило збудовані коксові батареї №№ 5, 6. Захід зібрав багато промислових фахівців, науковців, колег з інших підприємств України. Гості наголошували на унікальності події, і це дійсно було так.


Протягом п’яти років продовжувалась реконструкція комплексу коксових батарей № 5-6, до якої входили також деякі об’єкти вуглепідготовчого цеху та цеху уловлювання. Старі батареї були зупинені ще у квітні 2013-го. За терміном експлуатації та їх технічним станом КБ вже неможливо було експлуатувати.
Щоб збудувати нове, треба було позбутися старого. Будівництво нових КБ стартувало із величезного за своїми обсягами демонтажу старого обладнання. З робітничого майданчика прибирали усе, навіть старий фундамент коксових батарей. Паралельно з цим «кипіла» робота над проєктом сучасних КБ. Будівництво виконувалося у два етапи – спочатку в експлуатацію увійшла коксова батарея № 6, а вже потім КБ № 5. Проєктна потужність нових КБ №5-6 склала 530 тис. тонн валового коксу на рік кожна.

Без пилу та газів
Ви колись хотіли дізнатися, як влаштований механічний годинник, як його маленькі гвинтики, пружинки рухають стрілки так, щоб ті завжди показували нам точний час?
Ось і щоб дізнатися як працюють нові коксові батареї №№ 5,6, чому вони екологічніші та ефективніші за свої «колег», варто теж дізнатися як вони влаштовані, за яким принципом працюють. Розібратися з цим нам допоможе Ярослав Дячук, заступник начальника коксового цеху № 1 КХВ.
«Сучасні екологічні та технічні рішення були впроваджені на КБ ще під час проєктування, – розповідає Ярослав Дячук. – Нові батареї більш газощільні, що виключає втрати газу, а рівень запиленості та загазованості повітря робочої зони знижено на 30%.
У рамках проєкту були збудовані нові пилоочисні установки в дробарному відділенні вуглепідготовчого цеху та на коксосортувальні у коксовому цеху.
Одне з важливих нововведень – технологія попереднього трамбування та бездимного завантаження шихти. Вона обумовлює формування «трамбованого пирога» з вугілля ззовні коксової печі. Їх ущільнюють спеціальними молоточками. Після цього вугільний «пиріг» з такими ж розмірами, як і у камери коксування, завантажується у піч. Слід зазначити що це дуже великий за розмірами «пиріг»: довжина його – майже 15 м, висота – 4,8 м, а ширина – майже пів метра, вага такого «пирога» складає майже 37 т. За допомогою трамбування насипна щільність шихти збільшується до 35 відсотків, а продуктивність печі – на 10-12 відсотків. Крім цього, ми ще можемо економити, адже технологія попереднього трамбування шихти дозволяє використовувати дешевші вуглі. Головна фішка у тому, що якість виробленого коксу при цьому значно покращується.
Була вдосконалена і конструкція кладки та армування печей для запобігання перетіканню сирого коксового газу з камери коксування в опалювальні простінки. Це дозволило мінімізувати шкідливі викиди від горіння через димохід коксових батарей. Завдяки використанню гідроінжекції – системи, яка втягує газ у спеціальні газозбірники, кількість викидів забруднюючих речовин при завантаженні камер коксування знижується. Не давати шкідливим газам виходу з коксових печей дозволило і застосування газощільних дверей удосконаленої конструкції з гнучкими ущільнювальними рамками. А ущільнення кришок та раструбів стояків азотом дозволило максимально мінімізувати викиди зверху коксових батарей».

На нових КБ була впроваджена безпилова видача коксу. Тепер, коли кокс потрапляє до тушильного вагона, коксовий пил вже не розлітається. Він уловлюється димососами та далі проходить очищення через фільтри.
Модернізувався і процес мокрого гасіння коксу. Коли його гасять водою, виникає та сама біла пара, яку періодично бачать мешканці нашого міста. І це випаровування без наявності у своєму складі брудної води. Адже всередині нової башти гасіння коксу поставили спеціальні каплевідбійники, які і затримують воду.
Реалізація проєкту реконструкції коксових батарей №№ 5, 6 дала значний екологічний ефект – зниження викидів на 1600 тонн на рік за проєктною продуктивністю коксу. Нові технології, спрямовані на зниження викидів пилу та газів, були впроваджені на усіх стадіях виробництва коксу – починаючи від завантаження шихти, коксування, і до видачи готової сировини.

Як зазначила Людмила Руднєва, заступниця директора департаменту зі сталого розвитку нашого підприємства: «Впровадження сучасних технологій на КБ №№ 5, 6 дозволило на 26 % зменшити неорганізовані викиди забруднюючих речовин при завантаженні. Також на 100 % були виключені неорганізовані викиди забруднюючих речовин при коксуванні вугільної шихти. Завдяки збудованій установці безпилової видачі коксу, у процесі його видачі викиди знизилися на 95%, досягнута концентрація по пилу становила 35 мг/м3. На 59 % були знижені і викиди при сортуванні коксу.
Хочеться відзначити, що на нових коксових батареях були збудовані автоматизовані системи екологічного моніторінгу, а саме встановлені пиломіри та газоаналізотори, які дозволяють відслідковувати інформацію про обсяги викидів оксиду вуглецю, окислів азоту, діоксиду сірки та запиленості».

«Здача на права», щоб керувати батареями
На нових коксових батареях було встановлене сучасне німецьке обладнання. Тут автоматизовані виробничі процеси з обслуговування коксових печей і основного технологічного обладнання. Це дозволило значно знизити тяжкість праці коксохіміків. А нова припливно-витяжна вентиляція та система кондиціонування забезпечують ефективний обмін повітря у виробничих приміщеннях.
Старі кнопки та гачки на здійснення кожної виробничої операції замінили сенсорні екрани. Тепер все стало, як на смартфоні. А саме на екрані комп’ютера машиніст знаходить потрібну дію, наприклад, зняття дверей, проводить пальцями по екрану, і виробничі процеси на коксових машинах автоматично розпочинаються.
Для здійснення усіх процесів на коксових батареях фахівцям першого коксового цеху треба було пройти спеціальне навчання. З новим обладнанням наших спеціалістів знайомили представники фірми-виробника. Теоретичні заняття проходили в Університеті АрселорМіттал, а практичні – на будівництві нових коксових батарей. Це було дуже корисним, адже фахівці мали унікальну можливість на власні очі побачити, як влаштоване обладнання зсередини, як воно збирається, монтується тощо. Такі знання вже потім суттєво допомогли коксохімікам у роботі та при обслуговуванні коксових батарей.

«Нам треба було мати справу з найновішим обладнанням, це був новий рівень у техніці: автоматизація, повно нової електроніки, гідравліка, система змащування, компресори. Ми опановували тромбування коксового «пирога», під керівництвом німецьких кураторів, засвоювали й інші виробничі операції. Було складно, але потім, коли розібралися, навчилися, то навпаки, працювати стало легше, бо обладнання саме тобі у всьому допомагає», – ділиться спогадами Віталій Гуменюк, майстер з ремонту механоустаткування КБ №№ 5, 6.
«Були встановлені нові для нас різноманітні датчики, частотні перетворювачі та інше обладнання. Щоб обслуговувати та ремонтувати все це нам треба було добре з цим познайомитися. Німецькі спеціалісти нам у цьому допомогли, та й в інтернеті довелося чимало посидіти, переважно ми знайомилися і з технічними характеристиками обладнання. У перший день роботи на нових КБ ми з колегами були трохи на стресі, але згодом все стало на свої місця, – розповів Олександр Вовк, в.о. майстра з ремонту електрообладнання.
«На підприємстві я працюю з 1993 року, тож досвід був, але на новому обладнанні було все інше, – зазначив Тарас Василів, машиніст електровоза тушильного вагону. – Одразу, з чим зіткнувся – багато електроніки. Воно, звичайно на краще, бо ти переважно задаєш необхідні операції, наприклад, на видачу, на башту гасіння та контролюєш їх. Але цьому треба ж було навчитися, і потім добре виконувати все, бо хибити у нашій справі категорично не можна. Зараз мені легко працюється, я знаходжусь у кабіні, яка захищена від пилу та газів, кондиціонується, контролюю роботу і витрачаю енергію лише на увагу, безпеку праці та дотримання технологічного процесу».

Стрес для людей та батарей
Через початок повномасштабного вторгнення робота комплексу коксових батарей №№ 5, 6 на КХВ була призупинена. Ворог дуже швидко просувався до Кривого Рогу, тож у персоналу коксового цеху № 1 було багато задач: вистояти морально і фізично, а також зберегти виробництво. Коксові батареї були поставлені на «гарячу консервацію». Це коли вже пусті, без коксу, камери коксування закриваються, ущільнюються, аби туди не потрапляло повітря, та постійно підігріваються, щоб підтримувати відповідну температуру, бо повністю тушити працюючі коксові батареї не можна – це смерть для них. «Гаряча консервація» була для КБ чималим стресом, але нові батареї та персонал коксового цеху № 1 гідно подолали цей виклик. Працівники регулярно перевіряли технічний «стан здоров’я» коксових батарей, слідкували за їх температурним та гідравлічним режимами.
Спочатку КБ підігрівали за допомогою коксового газу, а коли виробляти його не стало можливості, вперше почали застосовувати природньо-азотну суміш – з цією ідеєю та обладнанням нашим коксохімікам допомогла корпорація «АрселорМіттал». Установку, яка виробляла цю суміш оперативно привезли з Польщі.

«Відновлювати роботу КБ №№ 5, 6 ми розпочали з третього жовтня 2022 року, – продовжує Ярослав Дячук. – Розпочали з шостої батареї. Ми відкрили заглушки засувок на газопроводі та почали вже процес завантажування КБ, до того ж вантажили відкритим стояком, щоб не було хлопка газу в газопроводах. Обладнання «ожило». П’ятого жовтня ми отримали перший кокс, цього ж дня було розпочало завантажування шихтою КБ № 5. Пам’ятаю, що настрій у всіх тоді був піднесений, всюди лунало: «Ми працюємо», а це дуже важливо в умовах війни. Але надалі на усіх нас чекали інші випробування – блекаути. Іноді у нас зникало світло, зупинялися деякі агрегати, але ж не усе одночасно та одразу! При першому блекауті спочатку була тиша, а згодом через тиск у коксових батареях газ почав шукати собі виходу. На щастя, до вибуху не дійшло, ми вчасно зробили все, що було передбачено планом ліквідації аварійних ситуацій – одразу зупинили подачу газу на обігрів КБ, перекрили засувки та утримували необхідний тиск до подачі світла. Подібні моменти ми переживали кілька разів. Але в останній блекаут, на жаль, коксова батарея № 5 все ж не витримала. На ній в момент зникнення світла саме відбувався процес завантаження, коли двері КБ були відкритими. Зараз КБ № 5 не працює, вона на «гарячій консервації», там проводиться ремонт. А ми працюємо на КБ № 6, яка забезпечує коксом виробничі потужності підприємства. Кожного дня ми продовжуємо свою справу та вирімо, що зовсім скоро будемо працювати на повну. Головне, щоб війна скінчилася, а там, незабаром, ми усі напишемо нові цікаві сторінки в історії наших нових коксових батарей».

