Трансформуватися, щоб не ламатися
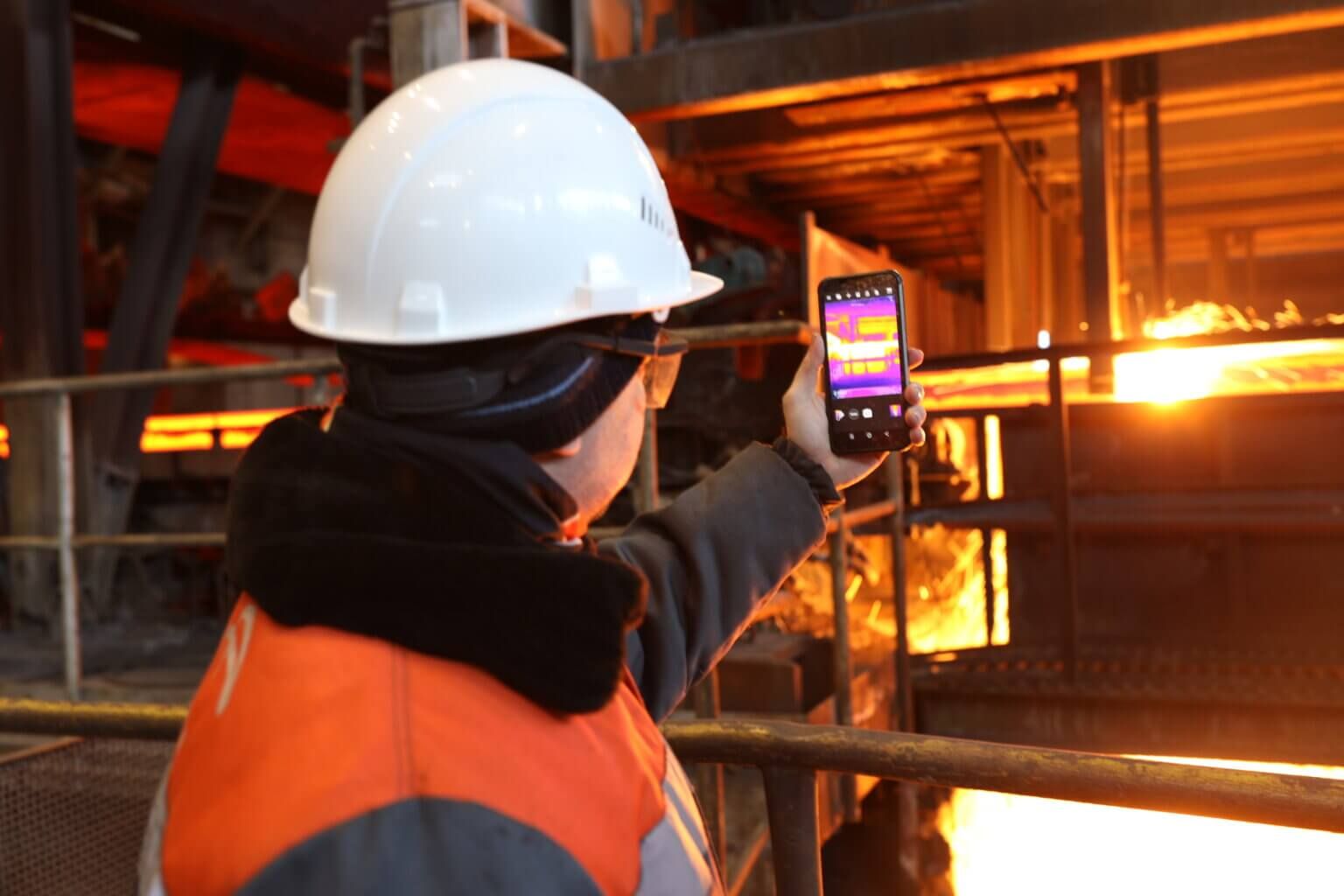
Серед технарів розповсюджена думка: чим простіший агрегат, тим рідше він виходить з ладу. Сучасне металургійне устаткування надзвичайно складне, і там є чому ламатися. Наприклад, відділення безперервного розливання сталі конвертерного цеху – це комплекс агрегатів, де тісно сплетене механічне, гідравлічне, енергетичне, електричне устаткування, робота якого координується і керується безліччю контрольно-вимірювальних приладів та автоматизованими системами керування технологічними процесами.
А ламатися цьому устаткуванню не можна, бо навіть у назві відділення є слово «безперервного». Для того, щоб максимально запобігти поломкам, у ВБРС конвертерного цеху триває процес трансформації системи технічного обслуговування та ремонтів. За словами керівника цього проєкту, начальника служби з ТО та ремонтів ВБРС Миколи Єфіменка, реалізація проєкту вже на завершальній стадії, ї є перші позитивні результати. «Принципова відмінність нової системи ТО і ремонтів – це її цілковита превентивна спрямованість, – пояснює Микола. – Тобто обслуговування та планові ремонти мають бути такої якості, щоб непрогнозовані поломки і аварійні ремонти виключити взагалі».
Проєкт з трансформації ремонтної служби – це ініціатива генерального директора нашого підприємства Мауро Лонгобардо. Така увага керівництва підприємства саме до ВБРС не випадкова. Адже саме це відділення виробляє високоякісні сталеві заготовки, які використовуються для виробництва арматури, катанки, кутника, смуги та інших видів нашої продукції, що дає левову частину прибутку. А філософія успішної роботи машин безперервного лиття заготовок саме в тому, що устаткування має працювати без простоїв, тобто жодних аварійних ситуацій не повинно бути.

«Якраз стабілізація процесу виробництва ВБРС, вихід на проєктні режими і мінімізація неконтрольованих поломок і стояли на меті, – констатує Микола Єфіменко. – Провідна міжнародна аудиторська компанія Enerkey вивчила нашу систему ТО та ремонтів і запропонувала кардинально її змінити. До впровадження проєкту структура ремонтної служби була стандартною з розподілом на механослужбу, енергослужбу, електрослужбу. А фахівці з контрольно-вимірювальних приладів та автоматизованих систем управління технологічними процесами й взагалі були з іншого департаменту. Коли виникала проблема у роботі устаткування, кожна зі служб вивчала її за своїм напрямком окремо, що значно затягувало процес вирішення проблеми. Згідно з проєктом було змінено структуру ремонтного персоналу, а саме було поєднано усі служби у єдину команду з одним спільним керівником та введено нові посади – техніки, які були об’єднані в технічні групи Їх завдання – слідкувати за станом устаткування, планувати обслуговування і ремонти та своєчасно виявляти недоліки, не допускаючи поломок на ввіреному устаткуванні».
У ВБРС створили сім таких груп. До складу кожної групи входять техніки, які спеціалізуються на різних видах устаткування (механіка, енергетика, електрика і т.д.). За кожною групою закріплена певна кількість обладнання. Це дає значні переваги. По-перше, група з різних техніків швидше і точніше виявляє недоліки й приймає колегіальні рішення із врахуванням усіх нюансів. А по-друге, кожна група спеціалізується на певних агрегатах, тому знає їх більш досконало, що також сприяє ефективності роботи. Великою перевагою проєкту є створення окремих денних механічних та електричних майстерень. Їхній персонал готує запчастини та вузли до встановлення, щоб оптимально використовувати час планових ремонтів, не витрачаючи його на підготовку.
«Для завчасного виявлення недоліків ми отримали кілька нових можливостей, – продовжив Микола Єфіменко. – Серед них вібромоніторинг та термографія. Ці дослідження для нас виконують фахівці центрального департаменту з утримання та ремонтів і ПП «Стіл Сервіс». Для прикладу, використовуючи методи вібромоніторингу та термографії ми можемо завчасно виявити відхилення в роботі роторів газоочисної системи ВБРС та своєчасно виконати їх обслуговування, не допустивши аварійного виходу з ладу. Використання системи SAP є невід’ємною частиною проєкту та реалізується при підтримці спеціалістів служби ARMP, – пояснює Микола Єфіменко. – А це дозволяє нам зберігати величезні обсяги корисної інформації щодо результатів обстеження, виходів з ладу устаткування, відхилень в роботі, використання запасних частин, ремонтів, результатів діагностики та моніторингу тощо. Аналізуючи це, ми розробляємо шляхи вдосконалення системи ТО і ремонтів, беручи до уваги попередні недоліки та помилки».

Процес трансформації вже дає позитивні результати. Наприклад, з ініціативи технічних груп під керівництвом Антона Савенкова та Дениса Перепаденка було вдосконалено пневматичну систему керування машинами газової різки та маркувальними машинами. Технічні групи під керівництвом Андрія Ніколаєва та Євгена Очкася впровадили систему аварійної видачі плавок у випадках аварійних відключень електроенергії. Технічна група під керівництвом Олега Окорокова розробляє проєкт поліпшення системи охолодження гідравлічної системи МБЛЗ-1. Технічна група на чолі з Михайлом Кириченком виконала комплекс робіт з підвищення надійності трубопроводів підживлювальної води. Технічною групою під керівництвом Сергія Федорова реалізується проєкт безперервного заміру температури сталі у промковші. Ми ставимо на меті відпрацювати усі аспекти нової структури та сформувати ефективну службу. А в планах – трансформація системи ТО та ремонтів усього конвертерного цеху».