Як приготувати чорний пиріг з агломерату
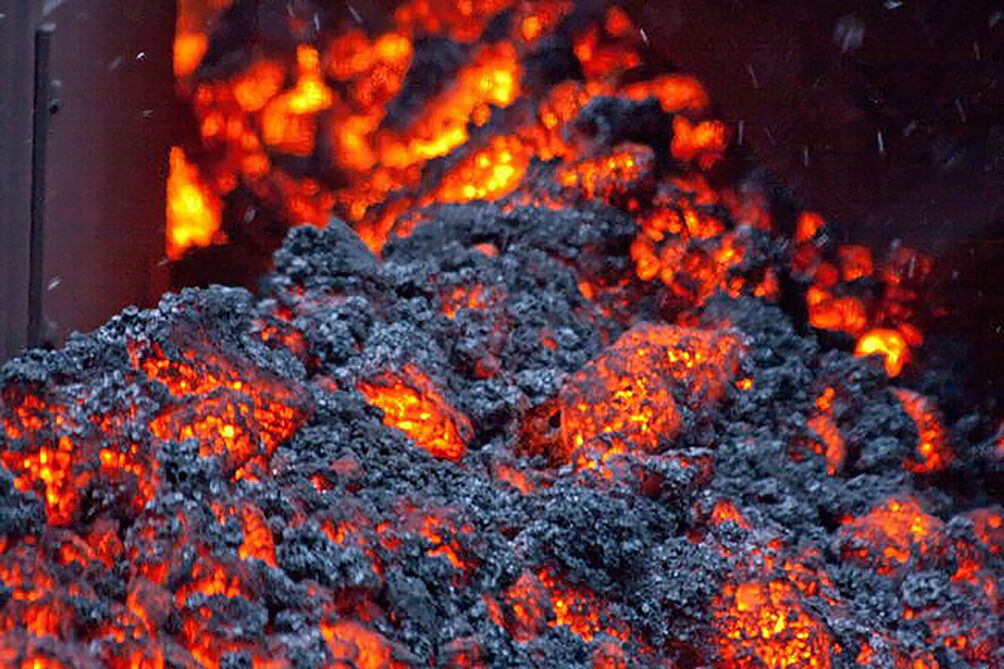
Агломераційне виробництво – своєрідний перехід від гірничо-збагачувальних до металургійних процесів. Саме тут завершується підготовка залізорудної сировини для виробництва чавуну і печуться гарячі чорні агломератні пироги.

Що ж таке агломерат? Його основа – це дроблена і потім збагачена залізна руда, тобто залізорудний концентрат – майже чорний пил, який здатен розлетітися від потоків повітря. Щоб ці крихітні часточки трималися купи, концентрат спікають у шматки на агломераційних фабриках. Його змішують з різними додатками, сильно нагрівають і за допомогою гарячого повітря підтримують необхідну для спікання температуру. Навіть саме слово «агломерація» походить від латинського agglomero – тобто приєдную, накопичую.

Якщо вдатися до історії, то агловиробництво стало відоме з кінця 19 століття. Винахід цього процесу пов’язують з англійцями Ф. Геберлейном і Т. Хантінгтоном. У 1887 році вони отримали патент на «екзотермічний процес огрудкування пилуватих руд у змішуванні з коксом, що здійснюється шляхом просмоктування повітря через шар зверху вниз».
Перша агломераційна стрічка називалася ґраткою. Вона почала роботу у 1906 році і використовувалася для спікання мідної руди.

Прорив у сфері огрудкування руд зробили два американські інженери – А. Дуайт і Р. Ллойд. У 1906 р. вони розробили конструкцію, а 1911 р. ввели у експлуатацію першу конвеєрну агломераційну машину безперервної дії у Бердсборо (штат Пенсільванія, США).
З того часу агломерація отримала широке промислове використання. Вона допомагала забезпечувати продуктивність доменного виробництва мінімум на 25-30 відсотків, впливала на інтенсивність плавки та дозволяла економити кокс щонайменше на 20 відсотків.

З того часу і до сьогодні без агломерату неможливо виробити чавун, адже він є однією з головних його складових. Тому можна сказати, що від якості агломерату безпосередньо залежить і якість металу, який виробляє наше підприємство.
Aглокухня «АрселорМіттал Кривий Ріг»

В «АрселорМіттал Кривий Ріг» агломерат для доменних печей виробляють чотири агломераційних цехи. Найстарший з них – аглоцех металургійного виробництва – почав роботу в далекому 1951 році. В період з 1960 по 1962 роки запрацювали ще три – №№ 1, 2, 3, які на той час були у складі Новокриворізького гірничо-збагачувального комбінату і доєдналися до нашого підприємства у 1996 році. Напередодні війни, у січні 2022 року, цехи виробили майже 850 тисяч тонн агломерату для трьох доменних печей.

Як готують пироги з агломерату, ми дізналися від досвідчених металургів.
Старший змінний майстер агломераційного цеху № 2 Олександр Петров за 22 роки роботи вже на відмінно вивчив кожен етап виробництва . Олександр водить нас «вулицями», «провулками» та «дворами» свого цеху, показує його велетенські агрегати та комунікації, розповідає про квіти, турботливо висаджені на клумбах та в горщиках робітниками. Працівники цеху кажуть, що тут навіть білки бігають, випрошують в агломератників горішки та інші смаколики.
«Останні кілька років наш цех значно реконструювали, – розповідає Олександр Петров. – Це помітно навіть неозброєним оком. Корпуси газоочисток блищать, нові установки працюють, як годинники. А бетонні майданчики біля виробничих дільниць регулярно миють водою зі шлангів – гарненько, під тиском, щоб пилу під ногами не було! Брудна вода теж стікає «з розумом» – спеціальними стоками, а далі у… «Байкал». Так між собою робітники жартома називають шламосховище, куди надходить уся вода, що була використана у виробництві».
Замішуємо основні інгредієнти
На першому пункті агломераційної «пекарні» – дільниці з вагоноопрокидувачем агломераційного цеху № 3 нас зустрів змінний майстер АЦ № 3 Олександр Заїка.

Саме в аглоцеху № 3 замішується правильне «тісто» для подальшого успішного випікання аглопирога. «Залізничними складами до нас привозять шихтові матеріали – основні інгредієнти: різного виду вапняки, кокс, вугілля, аглоруду. Вивантаження їх відбувається за допомогою вагоноопрокидувача. Вагон розміщується всередині спеціального ротора, міцно затискається і перевертається. Сировина висипається на спеціальну решітку приймального бункеру. Потім мережею конвеєрного транспорту сировина спрямовується на склад шихтових матеріалів», – розповів фахівець.

Перше, що впадає в око на цьому відкритому складі – величезні конусні піраміди сировини, кольорові купи: руда купа – це аглоруда, чорна – коксова дрібниця, сіруваті – вапняки тощо.

Зі складу сировини сипкі матеріали подаються на дроблення. Дробарки розбивають грудки продукту: вапняки, паливо (коксову дрібницю) або вугілля. Це роблять п’ять молоткових дробарок та вісім чотирьохвалкових. «Що і де дробиться, можна визначити по кольору дробарок. Де вапняк, вони аж білі, чорні – де подрібнюється паливо», – говорить дробарник Андрій Рогалін.

На наступному етапі грохочення матеріал висипається на спеціальні сита і розділяється за розмірами шматків або частин (фракцій). Фракція гідного вапняку, який іде на дозування, за розмірами складає від 1 до 5 мм, інше повертається і знову проходить увесь ланцюг обробки.

Дозуємо – і в «блендер»
Щоб спекти якісний агломерат, усі складові шихти потрібно ретельно відміряти, тобтозважити та видати у потрібних пропорціях.
«Компоненти шихти транспортуються конвеєрами до корпусу шихтових бункерів – розповідає Олена Хібіна, старший майстер основної виробничої дільниці АЦ № 3. – До речі, довжина конвеєрів нашого цеха складає майже 15 кілометрів. З операторського пункту керується робота конвеєрного транспорту, вагодозаторів, тарілчастих живильників, автостел. Потрібна кількість сировини потім транспортується до першого та другого агломераційних цехів для подальшого виробництва».

Відомо, що під час приготування будь-якої страви чи не найголовнішу роль грає змішування. У виробництві агломерату так само: усі компоненти потрібно ретельно змішати, щоб склад сировини став максимально однорідним. Інакше спікання буде неможливе.


Розподіляємо та відправляємо у піч
Після змішувальної «каруселі» готова шихта конвеєром їде до корпусу спікання. Там вона розподіляється по бункерах кожної агломераційної машини. В першому і другому аглоцеху їх по шість.

До речі, корпуси спікання – це доволі високі споруди. Висота у найвищих точках дорівнює майже дев’ятиповерховому будинку, але ці будинки мають дуже складну «начинку» з різних агрегатів. Головні з них, звичайно, агломераційні машини. Це своєрідні духовки з рухливою стрічкою спікальних візків, на які безперервно рівним шаром завантажується агломераційна шихта.
«Коли шихта надходить до бункерів агломашин, вона дозується живильниками до вторинних змішувачів, – пояснює Олександр Петров. – Туди подається вода для зволоження шихти та газ для її підігріву. Температура перед спіканням має бути 52 градуси за Цельсієм. Потім шихта огрудковується і з пилоподібного матеріалу утворюються вологі грудочки розміром 3-12 мм, так шар шихти стає газопроникним. Завантажена на візок частина вирівнюється «гладилкою» і прямує під запалювальний горн».
Рухаючись по рейках візок проходить крізь запалювальний горн, де спалюється газ, який у свою чергу запалює паливо у шихті. Крізь шихту за допомогою ексгаустерів безперервно просмоктується повітря. Температура в горні досягає 1150 градусів Цельсія. Тільки уявіть, приблизно така ж температура всередині мантії Землі або розжареної вулканічної лави! Завдяки горінню палива у шарі шихти, в ньому відбувається часткове відновлення залізної руди і спікання окремих грудочок матеріалів у більші за розмірами грудки готового агломерату.
Агломашинами і взагалі всім обладнанням керують оператори пульта керування. А безпосередньо процесом спікання опікується агломератник, він головний «шеф-кухар».
«Я контролюю процес спікання агломерату, визначаю подачу необхідної кількісті газу для запалення, підтримую необхідну температуру, вологість, подачу шихтових матеріалів, – розповідає агломератник Ігор Подколодній. – Допомагають прилади і досвід, бо працюю тут вже 15 років. Спочатку, коли тільки навчався, трохи боявся, чи впораюсь з процесом. Зараз почуваюся впевнено і вже навіть на око можу побачити, чого і скільки потрібно для спікання, та визначити якість агломерату».

«Пиріг», який добре пропікся, охолоджують у спеціальній зоні охолодження. Встановлені там вентилятори продувають агломерат і знижують його температуру з 800-1000 до 90-100 градусів. Готовий продукт скидають з візків, дроблять, відсівають на грохотах і відправляють до доменного цеху для виготовлення чавуну. А дрібні шматочки агломерату повертають в змішувач для підготовки шихти – вони наново пройдуть увесь процес обробки при приготуванні іншої порції «пирога» від «а» до «я».

Гідна альтернатива
Але агломерат – не єдиний базовий інгредієнт для чавуну. Зараз країни з розвиненою металургією мають високий інтерес до залізорудних окатишів, як до одного з основних видів сировини для доменного виробництва. Наприклад, у Швеції до 100% окатишів складають залізорудну частину доменної шихти, у США й Канаді – 70-80%.
Окатиші – це рудний матеріал, отриманий з дрібної (пилоподібної) руди або тонкоподрібнених концентратів, у вигляді кулястих гранул діаметром 2-3 до 30 мм (зазвичай 10-15 мм). Залізорудні окатиші застосовуються головним чином у доменній плавці.

Металурги розглядають залізорудні окатиші як якісну сировину, що наближається по однорідності властивостей до агломерату. Ця сировина здатна транспортуватися на будь-які відстані без втрат ними металургійних властивостей. До того ж, газопроникність їхньої насипної маси більша, ніж в агломерату. Та і сам процес їх виготовлення значно екологічніший.
Саме тому «АрселорМіттал Кривий Ріг» з жовтня 2020 року розпочало будівництво нової суперсучасної фабрики огрудкування. Цей проект є уособленням та важливим кроком компанії у напрямку «зеленої металургії» – виробництва зі світовими стандартами щодо рівня викидів та забруднення навколишнього середовища.

Передбачається, що нова фабрика огрудкування буде виробляти 5 млн тонн окатишів на рік, потужність за годину – 621 тонна. Там планується встановити потужні газоочисні та аспіраційні установки за європейськими екологічними стандартами.

Інвестувати у будівництво фабрики огрудкування компанія «АрселорМіттал» планувала понад 250 млн доларів. Так би воно і було. Перешкодила втіленню цих планів у життя війна. На сьогодні будівництво фабрики поки що призупинено. Найважливішим на часі є питання виживання підприємства і збереження трудового колективу.
Втім, будемо оптимістами. Війна обов’язково скінчиться, підприємство запрацює, а нові «зелені» проекти в агломераційному виробництві обов’язково будуть втілені в життя. Це зробить підприємство більш сучасним та ефективним.