Гуркоти, затвори і скіп з бігунами
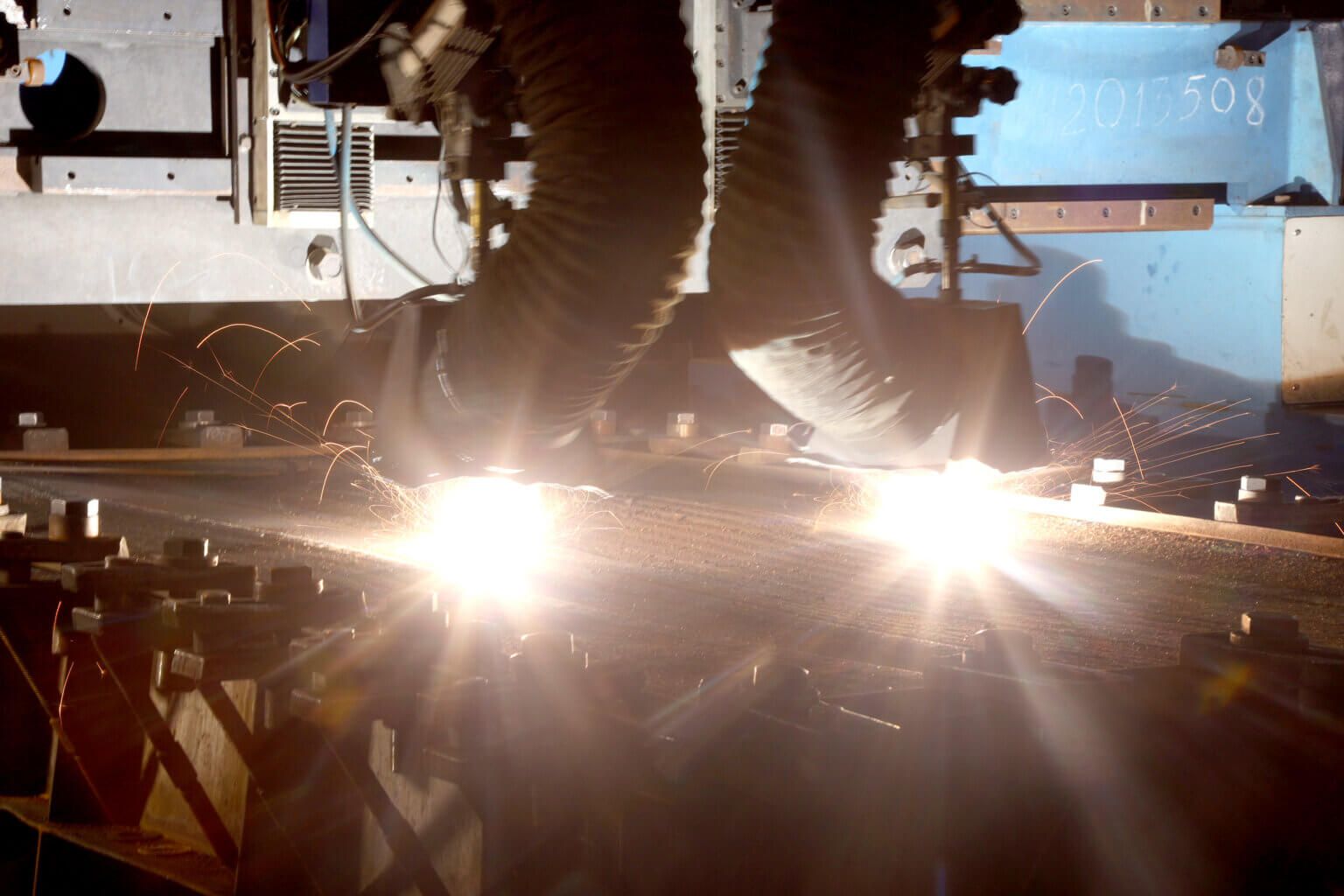
Капітально відремонтоване фахівцями Ливарно-механічного заводу устаткування для доменної печі № 8 справно виконує свої функції.
Працівники цеху металоконструкцій та ремонтно-монтажного цеху № 3 капітально відремонтували гуркоти коксу та агломерату, скіп для транспортування шихти, виготовили чотири затвори коксу і стільки ж затворів агломерату. Деякі роботи в межах цих ремонтів виконали працівники РМЦ-1 і РМЦ-2.


Гуркоти коксу й агломерату використовуються для сортування цих матеріалів перед виготовленням шихти для виплавки чавуну. Короби для них виготовили з біметалу, тобто сталі, наплавленої твердим зносостійким сплавом. Такий матеріал допомагає протистояти механічному зношуванню цих виробів та високим температурам. Наплавлення сталевих листів для гуркотів та інших виробів виконали у РМЦ-3. Потім їх відвезли до ЦМК і там розкроїли на необхідні деталі. Як розповів начальник ЦМК Микола Грицан, для різання біметалу використали машини плазмового різання та термічного різання.

«Біметал твердіший за звичайну сталь, тому важче ріжеться, – пояснив Микола Грицан. – Основні роботи були виконані саме з допомогою плазми, яка утворюється зі стислого повітря та електричного струму. З роботою добре впоралися газорізальники цеху Богдан Ганов та Руслан Глаголєв. Деталі для гуркотів і затворів ми передали знову до РМЦ-3, а корпус для скіпа, який подає шихту з шихтового двору на верх доменної печі, зварили наші зварники Олександр Тинок, Євген Обжелянський, Ігор Струц, Артем Корнілов, Мирослав Романчіч».
Збирали гуркоти і затвори працівники РМЦ-3. Як розповів начальник цього цеху Андрій Караман, у гуркотах здебільшого використовувалися болтові з’єднання. Це дозволяє їм витримувати величезні навантаження під час просіювання матеріалів.

«Усередину виготовлених коробів ми вставили решітки для просіювання, а також приводи, які приводять їх у рух. Виготовленням гуркотів та затворів займалися бригадири слюсарів-ремонтників Василь Машошин, Андрій Зальотов, а також газорізальники Андрій Рошка та Євгеній Чевичелов, електрозварник Василь Ярема, старший майстер Сергій Разживін та інші. Але спочатку фахівці проєктного відділу ЛМЗ створили технічну документацію разом з кресленнями на гуркоти», – сказав Андрій Караман.
Скіп – це складний виріб. За суттю це залізничний вагончик, який рейками витягається на верх ДП-8. Він має так звану упряж, за яку зачіпляється. А ще упряж бере участь у розвантажуванні шихти в засипний пристрій печі, який також виготовили в ЛМЗ. Виготовляли упряж в РМЦ-3, а от механічну обробку корпусу скіпа виконали у РМЦ-2. Скіп має колеса, які називаються бігунами. Вони виготовлені зі сталі, міцнішої, ніж у звичайних залізничних коліс, тому заготовки для бігунів довелося купити, а от заготовки для осей викували на ковальській дільниці РМЦ-1. Обробили їх і отримали готові запчастини працівники РМЦ-3. «Збиранням скіпа займалися бригадир слюсарів-ремонтників Юрій Шибилист, слюсар-ремонтник Віталій Удалов, електрозварник Віталій Стовба, газорізальник Валерій Курило та їх колеги», – додав Андрій Караман.

А бригадир Юрій Шибилист зізнався, що найскладніше було футерувати задню частину візка біметалом. Виготовлення й футерування корпусу скіпа біметалом має продовжити термін його використання. Електрозварник РМЦ-3 Володимир Кулак був серед тих, хто виконував наплавлення.
«Я ще тільки опановую роботу на наплавлювальній машині, – розповідає Володимир. – Хлопці, які раніше на ній працювали і написали програми для неї, зараз воюють. Тож хочу скористатися нагодою і передати їм найкращі побажання. Дмитро Магльований та Максим Гнідаш, величезна вам подяка за те, що нас захищаєте! А ми намагаємося тут в цеху вас не підводити. Чекаємо вас з перемогою!»